THE MG |
|
 |  |  | July 17, 2010 - Here's a peek at the differential from the Camaro. In 1998, the Z28 came with a Positraction differential. In 1999, that was changed to a Torsen. This is a Posi, although I do have to admit to resorting to Google to make sure I wasn't looking at some sort of Phantom Grip nastiness.
Miatas used Torsens from 1994, and it's a great differential. Very easy to drive. But the V8 cars we've been building at Flyin' Miata have been using a differential from a Cadillac CTS-V, and I've been very impressed with their ability to lay down power. The theoretical increase in turn-in understeer hasn't been a problem. I'm pretty sure it's a very similar Positraction to this one. So I'm happy that my donor came with this unit. entry 354 - tags: differential, rear axle |  |  |  | July 18, 2010 - Progress! Although it doesn't look like it. I pulled the engine and transmission out one more time. This will let me finish the sheetmetal work in the engine bay and elsewhere in the transmission tunnel. I'll also finish some welding on the frame and then paint everything.
Meanwhile, the transmission has to come off so I can change the lines to the slave cylinder. The sealed one-piece setup from the Camaro isn't going to work, so I'm going to do something similar to the setup used by Flyin' Miata. The MG master is the right size (lucky!) and so I just need to find the right banjo bolts.
Once the chassis is prepped and ready, I'll stuff the engine back inside for what will hopefully be the final time! entry 355 - tags: assembly, clutch |  |  |  | July 20, 2010 - Welding time! I've started to panel the engine bay. This will increase the rigidity of the front end, which is my primary goal. You can see the right front corner (on the left in this picture) is done, including some special bulges to clear the control arm. The left rear is also done, leaving a large hole for the headers to pass through. I could make this hole smaller, but then I'd only be able to remove the headers when the engine is out of the car. I can see that particular problem coming back to bite me! For a bit of extra strength, there's also a 1" square tube along the top of the left rear plate.
You can also see the unusually shaped motor mounts, including the one that has to reach over the steering column. Or at least, you could if I'd managed to take the picture in focus.
The engine bay looks pretty awful right now with all the different colors. I also have to admit that some of the welding to the original sheetmetal is not well done. But it'll be strong enough, and a bit of time with the grinder, some seam sealer and a POR-15 paintbrush will make it all look good. First, I have to finish some more patching and a bit more bracing. entry 356 - tags: engine bay, sheetmetal |  |  |  | July 27, 2010 - More welding. I was hesitant to add this photo, as it shows some pretty ugly welding. I cut that front plate a bit too short and had to do some filling in with the welder. It's not structural and it'll look fine when ground down, but it sure looks nasty right now. At least the important stuff is good.
Anyhow, the sheetmetal in the engine bay is moving along. I still need to add some reinforcements and patches in various places, as sharp eyes will attest. It's hot, dirty work, but it's pretty rewarding. entry 357 - tags: sheetmetal |  |  | 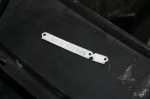 | July 27, 2010 - I had to move the VIN plate on the car. The intake tube wants to go through the middle of it. It was covered in 2-3 layers of paint and looked pretty nasty, so it got a quick trip through the bead blaster. Voila! entry 358 |  |  | August 4, 2010 - More welding. It's hot and dirty work doing the fabrication and welding in the engine bay and under the car, but I'm gradually getting through it. The engine bay is almost completely paneled now, but I still have to do some finishing. Then it's underneath to finish up some frame rail work.
I did pick up the rear axle from the driveline shop today, though. All new bearings, all set up with the Positraction rear. All I need to do is stick the axles in, mount the brakes and voila, that's done. It wasn't a cheap visit to the driveline shop, but at least I know everything's done right and I shouldn't have to do anything to it for a long, long time. entry 359 - tags: axle, differential, fabrication |  |  |  | August 12, 2010 - Welding, welding, welding. I'm working my way through the car, finishing up all the half-welded sections and fabricating patches for the various holes I had to cut. Some of that work is pretty complex, too - this section of the driver's footwell is assembled out of 9 pieces, including one that wraps around into that big circular cutout for the steering column. Some of the welding isn't pretty. That's what happens when you're trying to work inside/under a car that's on jackstands and hasn't been bead-blasted to nice clean metal. This was some awkward work. I actually sat on the steering rack for some of it.
The good news is that I'm almost done! I just have to finish welding in part of the transmission tunnel and I can move on. entry 360 - tags: fabrication |  |  |  | August 12, 2010 - All of the seams on the cockpit will be sealed with seam sealer to ensure they're air/water tight. Some of the others in the engine bay - like this one - will simply get ground down before paint. Not all of them need to be, but the ugly ones do. The only piece of stock sheetmetal in this picture is the bit at the upper left with the leftover Aqua paint on it and a little bit at the upper right! entry 361 - tags: fabrication, engine bay |  |  |  | August 12, 2010 - While I was playing with the welder, I decided to take one more shot at welding the new rear frame rail to the bottom of the car. Previously, I'd found it almost impossible to weld the two together without burning through the floor. So the rail was attached with rosette welds through the top. But it just looked wrong when you peeked underneath.
With a different technique, I was able to make this happen. I'm much happier with that. entry 362 - tags: frame rails, suspension |  |  | August 16, 2010 - So, I had to wash the Bonneville salt off the M5. Janel and I went to Speed Week this past weekend. How cool is that? Anyhow, I took the opportunity to roll the LS1/T56 combo outside to clean it off as well. First, I pulled the coils off so I could get to the valve covers underneath. Then hosed the whole thing down with some degreaser and hit it with the hose.
Nothing too exciting, really. But the engine looks goooood! entry 363 - tags: engine |  |  |  | August 19, 2010 - The sheet metal work is basically done. There's still just a little bit of work to do once the transmission and rear end is back in, but it's time to start getting ready for the final drivetain installation.
The first step was seam sealer. This made me nice and messy, so I didn't take any pictures! But I sealed every seam that was involved in the interior - the footwells, the transmission tunnel and the ventilation system that had to be cut out and reassembled. So now the engine bay was black, green, rusty, bare and more black. Yuk. entry 364 - tags: fabrication |  |  |  | August 19, 2010 - A coat of paint made all the difference to the car. I used POR-15, my favorite rust paint. It's what I used on the Seven and Basil the Land Rover. I've found it to be tough and long-lived. It's also really easy to put on with a brush, flowing into a nice smooth coat and easy to touch up later. I use disposable chip brushes because it's almost impossible to clean them.
The end result looks good! Nice and shiny with a distinct lack of nasty surface rust. I painted the new metal under the car as well to protect it. I missed a few spots (of course!) and I have to move the jackstands to access a couple more, but overall it really looks good.
You can see the hole for the air intake in this shot as well. entry 365 - tags: paint |  |  |  | August 19, 2010 - I've also been playing with the engine. The most obvious is the new white headers. They were starting to pick up some surface rust sitting around the garage, so I grabbed a can of high temperature header paint to give them a nice coat. Black would have hidden the welding better, but I'm a sucker for white headers as followers of the Targa Miata know. I think they look awesome. Why paint and not ceramic? Because that's expensive and I've had pretty good luck with this paint. It'll do for now.
I also swapped the original Camaro intake manifold for my Corvette one. This isn't due to any sort of performance increase, but because I painted it to look like aluminum! Of course, it's not completely convincing. But it's a nice change from the usual black plastic and I think it'll look even better as it ages - ie, gets a little bit of dirt on it.
The Corvette manifold does have two differences, though. First, it doesn't have a hole for an EGR fitting, so I won't need to plug that. Good. Secondly, it doesn't have threaded holes for the throttle cable due to the drive-by-wire Corvette. Umm, bad. I'll fix that.
With the dressed engine sitting beside the painted rear axle and with the car freshly painted up, things are looking really nice! entry 366 - tags: engine, paint |  |  |  | August 23, 2010 - Exciting stuff - the fuel filler is in place. Well, actually, this is exciting. It means the gas tank is bolted into place for the last time. The assembly I'm doing now is final assembly, and that's the exciting part. Real progress: the pile of parts around the car is shrinking!
Originally, the fuel filler on the tank entered the trunk floor straight below the filler neck. You can see the patched and repainted hole in this picture - it'll be covered by sound deadening or carpet when the car is assembled. Since I had to move the tank over to make room for the exhaust, I had to make the filler wiggle over a few inches. A bit of back-room shopping at NAPA yielded a filler hose with a 45 degree angle. It worked out perfectly. entry 367 - tags: fuel |  |  |  | August 24, 2010 - The differential in its final home. Quite colorful! Hopefully, this will be the last glimpse of it I see for a while, it's time to button this thing up. entry 368 - tags: axle |  |  |  | August 24, 2010 - Before I can install the axles for the final time, it's time to put the studs in. I tried to overthink this and attempted to press them in with my big bench vice. Whoops - one broken vice. I couldn't get the geometry right to press them in with the press at work. So I figured I'd try what I considered the last resort and use a lug nut to pull them in. That spacer has a nice thick wall so it's strong, and the washer lets the lug spin against it.
And whaddya know, it was quick and easy. I hit the lug nut with the impact and the stud just sucked into place in a couple of seconds. Why did I try so hard? entry 369 - tags: axles, stud |  |  |  | August 24, 2010 - I found my driveshaft wouldn't give me the ability to get full droop out of my suspension. That's not good! The problem was two little bosses on the yoke at the transmission end. A couple of minutes with the die grinder and now I have a full range of motion all the way around. The bosses weren't structural as far as I can tell.
One step further! I did a bit more painting with POR-15 under the car tonight and did the final connections on the gas tank, so it's almost time to stuff that axle under the car and call it done. Well, I know it'll come out again for various reasons. But maybe not for a long time. entry 370 - tags: axle, driveshaft |  |  |  | August 29, 2010 - As promised (threatened? ), the rear axle has been installed. It's full of fluid, has the axles installed, brakes bolted up - it's all looking quite serious now! I still have a few things to do back here, such as working out how to make the Miata and the MG emergency brake systems and locate the platform for the bumpstop. You can see it here sitting on top of the axle. The bumpstop is installed on the chassis. I have to set things up so the bumpstop reaches full compression right before the shock bottoms out. Thus the lack of a spring, so I can do range of motion testing.
I pulled one of the bumpstops off a while back to play with it, and haven't been able to get it back on since. They fit over a mushroom shaped stud, so they have to deform to pop into place. Well, I finally got a brainstorm - I sprayed a bit of Simple Green on the bumpstop (great for lubricating exhaust hangers as well), held it in place, then used a jack to push the axle up. The axle pressed the stop into place with an easy little pop. Sometimes the thinking is much harder than the doing! entry 371 - tags: bumpstop, rear axle, brakes |  |  |  | August 29, 2010 - It's almost time to put the engine in. But first, I need to get at the slave cylinder. See, the Camaro uses a sealed hydraulic system and I need to mate it to the MG (or a different) master cylinder. It's also hard to bleed the system with the transmission mounted in a small car, or at least that's the fear. So I used the same setup that Flyin' Miata uses in their V8 Miatas. It's a new braided line with a banjo fitting on the end and a second long hose with a cap on it, used for bleeding. Easy enough - but I had to split the engine and transmission to do it.
The T56 transmission is a heavy beast, about 140 lbs. So I used a pair of jacks to hold it level as I pulled it free from the engine. And here's the first surprise - a Spec clutch. Normally, the smart thing to do when you've got your engine and transmission cracked apart is to put in a new clutch, but this one felt pretty good in the Camaro. So it's going to stay.
I thought there had been a change in slave cylinder designs, so I had a new one of the latest design ready to pop in. Well, turns out this car had the same design. It may have dated from the installation of the Spec clutch (remember, this engine was rebuilt about 30,000 miles ago) but whatever the reason, I may not have needed that new slave. Oh well, in it goes.
With the two-jack technique, the transmission slipped right on to the engine smooth as silk. It's never that easy. Which means something must have gone wrong. entry 372 - tags: transmission, clutch, slave, hydraulics |  |  |  | August 29, 2010 - Of course there was a problem. After I had the transmission all tightened down, I picked up the old slave cylinder and turned it over - and discovered this spacer hiding underneath. It's laser-cut steel, definitely not stock. It was probably installed with the clutch. Since the Camaro worked, it's also probably required as the old and new slaves are the same part number. So I had to pull the transmission out again. At least I was just working with an engine sitting on the floor!
Naturally, I ran into other problems. I pulled the slave off, installed the spacer and went to bolt it up again. And stripped out a thread on the aluminum transmission casing. With the spacer in place, there was less thread engagement. I ran a tap down the hole and dug through my collection of fasteners until I found a bolt that was long enough to make up the difference of the spacer. That worked fine, so then it was just a matter of reassembly. Sheesh.
Let's hope this all works! entry 373 - tags: transmission, hydraulics, clutch |  |  |
|